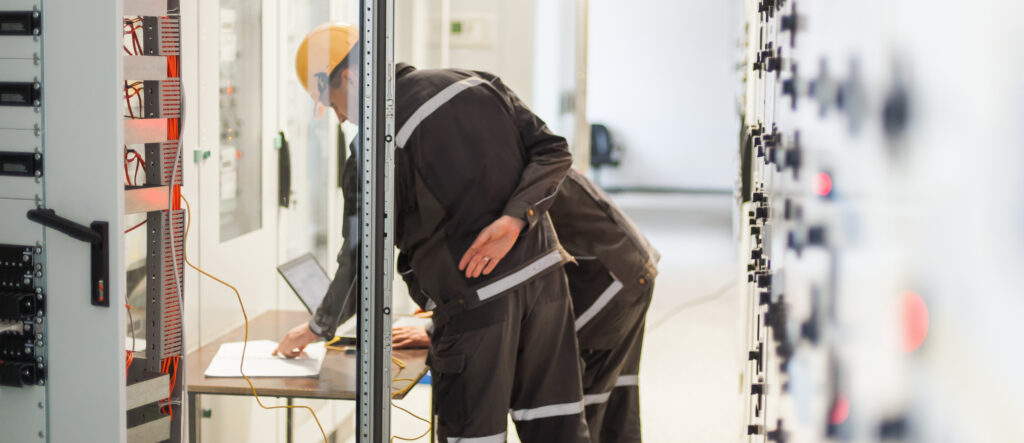
Seamless and Cost-Effective SCADA Upgrade
PUBLISHED ON Sep 01, 2021
Taking a Phased Approach Makes RTU and SCADA System Upgrades Seamless and Cost-Effective
Glades Electric Cooperative stages roll-out of new system after a comprehensive evaluation
Utilities that are replacing their aging remote terminal units (RTUs) and SCADA systems are doing so to ensure system reliability, improve usability and enhance future scalability – taking advantage of technology advancements in data connectivity and remote management. But how a utility approaches such a project is critical to ensuring that their system upgrade will be seamless and cost-effective.
Those who adopt a phased approach give themselves an opportunity to thoroughly evaluate the new technology’s feature set and assess its compatibility with existing equipment, which is critical for the extended process of transitioning to new technology. It also helps with the integration of new features so that a utility can take full advantage of what their new system offers. Staging the implementation is also a smart capital move as it does not commit project dollars before a thorough evaluation and go-forward implementation plan can be completed.
Glades Electric Cooperative, a 16-substation distribution cooperative that serves the power needs of four counties in Southern Florida with over 2700 miles of power lines and 17,000 meters, recently faced this challenge as they began their process of replacing their RTU and SCADA networks. Despite being installed relatively recently in 2015, the current RTUs were not meeting Glades’ reliability requirements.
“We were experiencing partial loss of function in one of our substations,” said Jose Cordova, Engineering Operations Manager at Glades. “One of the RTUs had four feeders, and there were times they would not respond to commands consistently. We also had a recloser that was not operating properly.”
Compounding the issue was virtually non-existent technical support from their vendor despite paying a fixed annual service contract above and beyond the product licensing fees. “We had service tickets that were months old that were never resolved,” said Cordova.
A contributing factor to Glades’ difficulty in resolving their technical issues quickly was their vendor’s use of a proprietary communications system between their RTUs and SCADA.
“The communication between the devices was proprietary technology, and so we were unable to resolve the issues on their own,” said Cordova. “When issues arose at a substation, it required us to deploy personnel to sort out issues manually, which eliminates the remote management benefits the system is supposed to deliver.”
So, when one of Glades’ RTUs in a substation failed completely in February 2020, they decided to search for a replacement from a new vendor.
The search for a new system
“We started our search for a replacement by surveying our system and establishing priorities based on what was not working or working less than optimally,” said Cordova.
Glades had three primary goals in mind with their replacement. Given the inconsistencies with their existing system, reliability was foremost in mind. Scalability was also a key criterion. They wanted a system that could grow with their network, which also meant the ability to integrate with peripheral devices at their substations. Finally, the new system needed to be user-friendly.
“Our typical substation has voltage regulators, transformers, and circuit switchers,” said Cordova. “We also have voltage regulators, capacitor banks, reclosers, and trip savers downstream. For maximum operability, we need all of these devices integrated into our SCADA system.”
Cordova added, “We have a team of nine, and not having to travel to update these devices saves us money, time, and most importantly, improves employee safety. We want to reduce how much time people spend directly interfacing with the equipment at our substations.”
Cordova attended a user symposium hosted by a leading substation automation provider, Pennsylvania-based NovaTech Automation, where he was introduced to the company’s Orion RTUs and SCADA systems.
“I attended a two-day class that included a demonstration of their system,” said Cordova. “I was able to work with some of their equipment and configure it, which was very informative. Having that kind of hands-on experience and access to product information enabled us to complete a thorough evaluation. One of the things we were impressed with was the intuitiveness of the Orion web interface.”
A stepwise implementation
Glades approached the replacement of their system in a phased, step-by-step approach beginning with the replacement of a single RTU. The idea was to connect an Orion RTU to their existing SCADA system to evaluate its performance and compatibility before making a more significant investment.
“We took advantage of the Orion RTU’s integrated online connectivity to serve up communications more efficiently,” said Cordova. “By typing the IP address of the new RTU, we could directly access it through a web browser to see the substation online.”
Based on this initial phase, Glades decided to move forward with a second RTU implementation.
About the same time, the second RTU was delivered to the next network location, a transmission station, the existing SCADA top-end failed unexpectedly, causing Glades to lose situational awareness at that location temporarily. Chronic technical support response time issues with the existing vendor-led Glades to decide to upgrade their entire system at this point – 16 substations and their SCADA top-end.
NovaTech addressed the need for situational awareness of the field through the SCADA system configuration. Devices in the substation serve up their own data on a graphic view. A top-end unit in the office governs all these units and allows a single viewpoint of the network without entering the IP address of each substation. To further improve efficiency, NovaTech installed an Orion SCADA server in the Glades’ IT room to act as a hub or data concentrator.
Today, Glades is about halfway through their co-op wide RTU replacement having installed Orion units at seven of their substations together with a data concentrator. When completed, they will have replaced their RTUs in all 16 substations.
Collaboration for optimal configuration
According to Cordova, the implementation has been very smooth despite executing the upgrade while working under the constraints of the pandemic.
The project scope included product, configuration, assembly services, testing, and site commissioning.
For the project, NovaTech assigned an engineer to build the system from scratch while working closely with Glades’ technicians.
“Having an expert involved helps us considerably because it enables us to customize as we build,” said Cordova. “This ensures that we have the features we need to make our operations center’s life easier.”
Cordova adds, “As an example, we have added an overview page that gives us a view of the entire system in one glance, eliminating the need to scroll through multiple screens to see what has happened at any of our 16 substations. If there’s an alarm, the overview page shows you exactly what happened and where in a very easy-to-understand layout.”
NovaTech is designing a load management page that will help Glades decide which feeders to turn off in a blackout rotation response to a volt electric emergency.
“With the latest advancement in technology, there’s so much more that can be automated. Many utilities are under-utilizing their systems simply by not turning on features that could eliminate manual interventions,” said Cordova.
“In our case, there was a lot of data that we could have been collecting that we were not,” said Cordova. “Bottom-line, we were simply not taking full advantage of what we had. So, this time, with the help of NovaTech, we have configured a much more useful and tailored product that also is much better supported.”
A cautionary tale
The lack of customer support that Glades experienced prior to selecting NovaTech resulted in a sub-optimized system configuration that created unnecessary manual work for their staff and increased their exposure to product failures because of the lengthy vendor response times.
Compounding the issue was that their vendor was charging a support fee through a service contract in addition to a significant annual product licensing fee. The support fee was charged as a fixed cost whether they serviced the technology or not.
With Glades’ new RTU and SCADA system, it is not only better configured to their needs providing more automation support and remote management capabilities, but there is no fixed support fee beyond the licensing cost. Glades pays for service only when they need it.
Stepping towards success
A technology upgrade is a significant project for a utility comprising configuration, assembly services, testing, and site commissioning. It is critical for a utility to take the time to fully assess the compatibility of a new technology with their existing systems, fully exploit new features to reduce manual interventions, and ensure licensing and support fees are to their advantage. Addressing these needs through a phased approach can help ensure an RTU and SCADA system upgrade will be seamless and cost-effective.